Are Stainless steel rivets stronger than Aluminum Rivets?
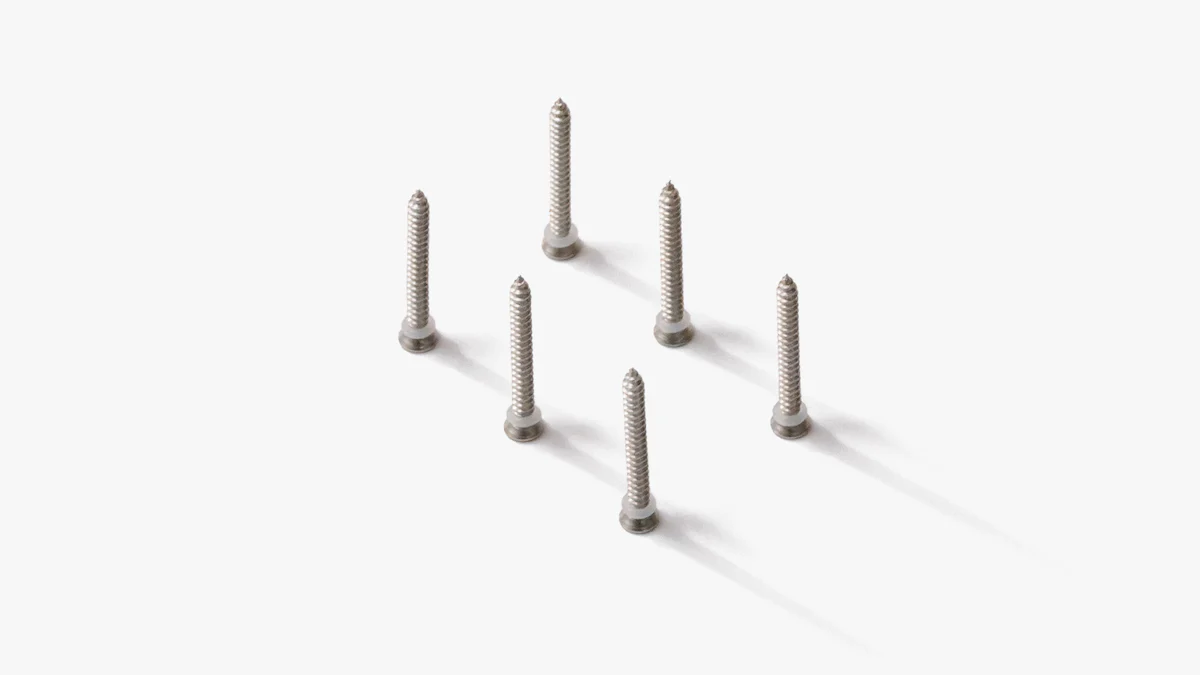
When choosing rivets for your project, you might wonder about the strength differences between stainless steel and aluminum rivets. Stainless steel rivets offer superior strength, making them ideal for heavy-duty applications. They provide excellent tensile and shear strength, ensuring durability in demanding conditions. However, aluminum rivets have their advantages too. They are lighter, which makes them easier to handle and install. Your choice between these two materials should depend on the specific needs of your application, considering factors like weight, strength, and environmental conditions.
Key Takeaways
- Stainless steel rivets provide superior strength and durability, making them ideal for heavy-duty applications.
- Aluminum rivets are lighter and easier to handle, making them suitable for projects where weight reduction is crucial.
- Consider environmental conditions: stainless steel excels in moist and chemically harsh environments, while aluminum performs well in less demanding situations.
- Evaluate both initial and long-term costs; while aluminum rivets are cheaper upfront, stainless steel may offer better value over time due to their durability.
- Assess your project’s specific requirements, including strength, weight, and budget, to choose the right rivet material for optimal performance.
Comparing Strength and Durability
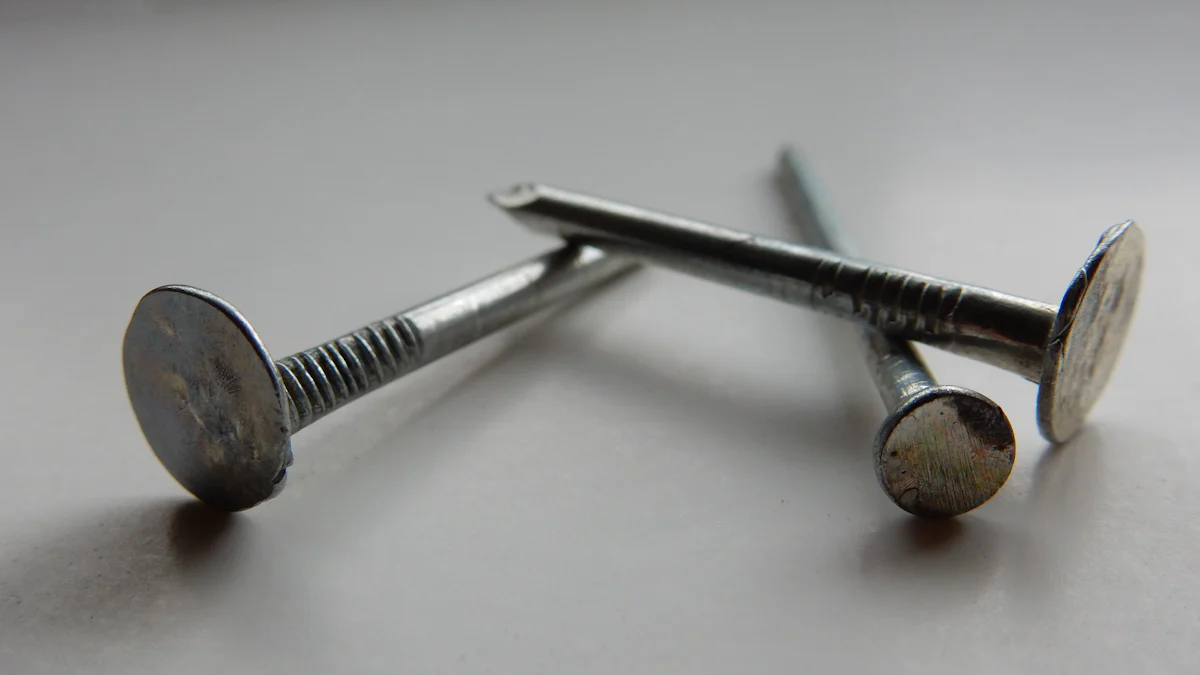
Tensile and Shear Strength
When you evaluate rivets for your project, understanding tensile and shear strength is crucial. Stainless steel rivets excel in both areas. They withstand high tension and resist forces that try to slide them apart. This makes them ideal for heavy-duty applications where strength is paramount. On the other hand, aluminum rivets offer a different advantage. While they may not match the tensile and shear strength of stainless steel, they provide a good balance of strength and weight. This makes them suitable for projects where ease of installation and handling are important.
Durability in Various Conditions
Durability plays a significant role in choosing the right rivet. Stainless steel rivets show remarkable durability in harsh conditions. They resist wear and tear, maintaining their integrity over time. This makes them perfect for environments that demand resilience. Aluminum rivets, however, offer durability in a different way. They perform well in less demanding conditions, providing a lightweight solution that still holds up under moderate stress. If your project involves exposure to varying conditions, consider how each material will perform over time.
Corrosion Resistance
When selecting rivets for your project, you must consider how they will perform in different environments. Corrosion resistance plays a crucial role in determining the longevity and reliability of your rivets. Both stainless steel and aluminum rivets offer unique advantages in this regard.
Performance in Moist Environments
In moist environments, stainless steel rivets shine. They resist rust and corrosion, maintaining their strength and appearance over time. This makes them an excellent choice for projects exposed to rain, humidity, or water. You can rely on stainless steel to hold up in these conditions without degrading.
Aluminum rivets, while not as robust as stainless steel, still offer decent performance in moist environments. They resist corrosion better than many other metals, making them suitable for applications where moisture is present but not overwhelming. If weight is a concern, aluminum rivets provide a lightweight alternative that balances corrosion resistance with ease of use.
Resistance to Chemical Exposure
Chemical exposure can wreak havoc on materials, but stainless steel rivets stand strong. They resist many chemicals, ensuring that your project remains intact even in harsh chemical environments. This makes them ideal for industrial applications where exposure to chemicals is common.
Aluminum rivets, on the other hand, have limitations in chemical resistance. They may corrode when exposed to certain chemicals, which can compromise their integrity. If your project involves chemical exposure, carefully consider the specific chemicals involved and how they might affect aluminum rivets. Stainless steel often provides a more reliable option in these scenarios.
Weight Considerations
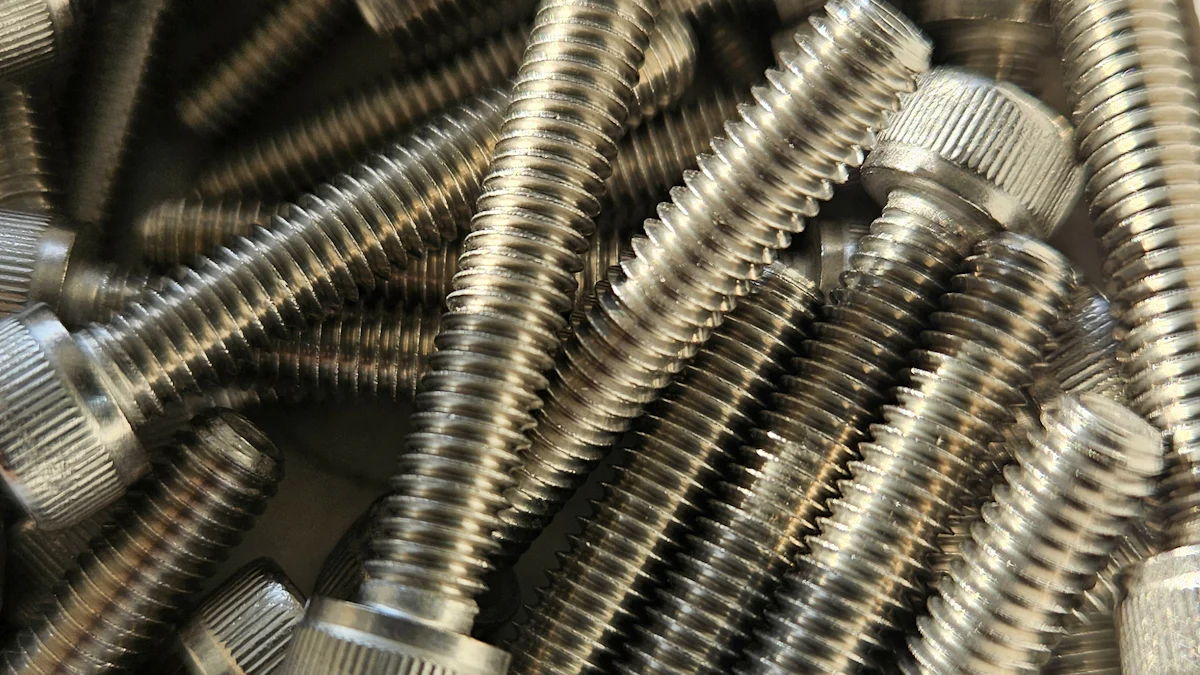
Impact on Overall Structure
When you choose rivets for your project, weight plays a crucial role. Aluminum rivets offer a significant advantage in this area. They are lightweight, which reduces the overall weight of your structure. This can be beneficial in applications where minimizing weight is essential, such as in aerospace or automotive industries. A lighter structure can improve fuel efficiency and ease of handling.
Stainless steel rivets, while heavier, provide unmatched strength. If your project demands high strength and durability, the added weight might be a worthwhile trade-off. Consider how the weight of the rivets will affect the balance and stability of your structure. In some cases, the increased weight of stainless steel rivets can enhance the robustness of the assembly.
When deciding between aluminum and stainless steel rivets, evaluate the specific requirements of your project. If weight reduction is a priority, aluminum rivets might be the better choice. However, if strength and durability are paramount, stainless steel rivets could be more suitable. Always weigh the pros and cons of each material to ensure the best outcome for your project.
Our factory NINGBO XIANGHAI KITCHENWARE CO.,LTD. manufactures a wide range of cookware Spare parts, such as Grill rack, induction disk, induction base plate, Induction Bottom Plate, Aluminum rivet, Flat head rivet, handle flame guard, weld studs, handle bracket, pan bracket, steel hinges, screw and washers, in order to provide our customers with the best quality products at the most competitive prices.
Cost Analysis
When selecting rivets for your project, understanding the cost implications is essential. Both initial costs and long-term expenses play a role in your decision-making process.
Initial Cost Comparison
Initially, aluminum rivets often present a more budget-friendly option. They typically cost less than stainless steel rivets. This makes them appealing for projects with tight budgets. If you need to purchase a large quantity of rivets, the cost savings can add up quickly. However, consider the specific requirements of your project. While aluminum rivets may save money upfront, they might not always meet the strength or durability needs of certain applications.
Stainless steel rivets, on the other hand, usually come with a higher price tag. Their superior strength and corrosion resistance contribute to the increased cost. If your project demands high performance and longevity, investing in stainless steel rivets might be worthwhile. The initial expense could lead to better results and fewer replacements over time.
Long-Term Cost Implications
Long-term costs involve more than just the initial purchase price. You must consider maintenance, replacement, and potential failures. Aluminum rivets, while cheaper initially, may require more frequent replacements in demanding environments. Their lower strength and durability can lead to additional costs over time. If your project involves exposure to harsh conditions, the long-term expenses of using aluminum rivets might outweigh the initial savings.
Stainless steel rivets, despite their higher initial cost, often prove more cost-effective in the long run. Their durability and resistance to corrosion reduce the need for frequent replacements. This can save you money on maintenance and repairs. In applications where reliability and longevity are crucial, stainless steel rivets offer a better return on investment.
When deciding between aluminum and stainless steel rivets, evaluate both the initial and long-term costs. Consider the specific demands of your project and how each material will perform over time. By weighing these factors, you can make an informed decision that balances cost with performance.
Choosing the Right Rivet for Your Application
Factors to Consider
When selecting rivets for your project, several factors come into play. Understanding these can help you make an informed decision:
-
Strength Requirements: Determine the load your rivets need to bear. Stainless steel rivets offer superior strength, making them suitable for heavy-duty applications. If your project involves high stress or tension, stainless steel might be the better choice.
-
Weight Constraints: Consider the weight of your structure. Aluminum rivets are lighter, which can be beneficial in projects where weight reduction is crucial. This is especially important in industries like aerospace and automotive, where every ounce counts.
-
Environmental Conditions: Assess the environment where your rivets will be used. Stainless steel rivets resist corrosion better in moist or chemically harsh environments. If your project faces exposure to such conditions, stainless steel provides a more reliable option.
-
Budget: Evaluate your budget constraints. Aluminum rivets often cost less initially, making them appealing for projects with tight budgets. However, consider long-term costs, as stainless steel rivets may offer better durability and fewer replacements.
-
Ease of Installation: Think about the installation process. Aluminum rivets are easier to handle due to their lighter weight. If ease of installation is a priority, aluminum might be the way to go.
Common Applications
Different applications call for different types of rivets. Here are some common scenarios where each type excels:
-
Stainless Steel Rivets:
- Construction: Ideal for building structures that require high strength and durability.
- Marine Environments: Perfect for boats and docks due to their excellent corrosion resistance.
- Industrial Machinery: Suitable for equipment exposed to harsh chemicals or high stress.
-
Aluminum Rivets:
- Aerospace: Used in aircraft manufacturing where weight reduction is critical.
- Automotive: Employed in car parts to improve fuel efficiency by reducing weight.
- Consumer Electronics: Utilized in lightweight devices where ease of assembly is important,also for some cookware.
By considering these factors and applications, you can choose the right rivet for your project. Each material offers unique benefits, so align your choice with your specific needs to ensure the best outcome.
When you choose rivets for your project, consider the unique benefits of each material. Stainless steel rivets provide exceptional strength and resist corrosion, making them perfect for challenging environments. They excel in applications where durability is crucial. On the other hand, aluminum rivets offer a lightweight and cost-effective solution. They are ideal for projects where weight reduction and budget are priorities. Evaluate your project’s specific requirements to make an informed decision. By aligning your choice with your needs, you ensure the best performance and value for your application.
FAQ
What are the main differences between stainless steel and aluminum rivets?
Stainless steel rivets offer superior strength and corrosion resistance. They are ideal for heavy-duty applications. Aluminum rivets, on the other hand, are lighter and easier to install. They suit projects where weight reduction is crucial.
Which type of rivet is more cost-effective?
Initially, aluminum rivets are more budget-friendly. However, stainless steel rivets may prove more cost-effective in the long run due to their durability and reduced need for replacements.
Can I use aluminum rivets in marine environments?
Aluminum rivets resist corrosion better than many metals, but stainless steel rivets perform better in marine environments. Stainless steel offers superior resistance to rust and corrosion, making it a more reliable choice for such conditions.
Are stainless steel rivets suitable for all applications?
Stainless steel rivets excel in applications requiring high strength and corrosion resistance. However, they may not be the best choice for projects where weight is a critical factor, such as in aerospace or automotive industries.
How do I decide which rivet to use for my project?
Consider several factors: strength requirements, weight constraints, environmental conditions, budget, and ease of installation. Align these with your project’s specific needs to choose the right rivet.
Do aluminum rivets require special tools for installation?
Aluminum rivets are generally easier to install and do not require special tools. Their lightweight nature makes them user-friendly, especially for DIY projects.
What are the common applications for stainless steel rivets?
Stainless steel rivets are commonly used in construction, marine environments, and industrial machinery. They provide excellent strength and corrosion resistance in these demanding applications.
Can I mix stainless steel and aluminum rivets in one project?
Mixing different types of rivets in a single project is not recommended. Different materials may react with each other, leading to corrosion or weakening of the joint over time.
How does the weight of rivets affect my project?
The weight of rivets impacts the overall weight of your structure. Aluminum rivets reduce weight, which can improve fuel efficiency and ease of handling in applications like aerospace and automotive.
Are there any maintenance considerations for rivets?
Regular inspection is essential, especially in demanding environments. Stainless steel rivets require less maintenance due to their durability, while aluminum rivets may need more frequent checks and replacements.
Post time: Dec-24-2024